Wax (redux)
Moderators: William Anderson, letumgo
Wax (redux)
Those of you who know me know I have a bit of a fascination with tying wax. I use it whenever I tie -- I keep a daub on the knuckle of my left index finger, a la Davie McPhail. Ray was kind enough, after I met him at a demo, to email me links for the various threads and recipes on this forum and elsewhere. Somehow, I was relatively successful in making a batch approximating the 6-2-2 forumla (6 parts rosin, 2 parts wax, 2 parts fat/oil -- I used mineral oil).
This is called winter wax -- I made this recipe in particular because, well, it was winter and I was tying steelhead flies. Now it's summer, and as those of you who use wax know, it gets rather runny and isn't particularly user-friendly, particularly in my overheated third-floor tying room. I've been using some cobbler's wax that Ray gave me, but it's quite dark. I've been meaning to whip up a batch of summer wax, and -- encouraged by the impending end of summer -- made up a batch last night.
I tried an 8-2-1 recipe I found in the archives, figuring it would be a little more heat-friendly than the usual summer 7-2-1... and all went well until the 'pull it like taffy stage' (which I hadn't done to my batch of winter wax). To make a long story short, I found myself in a battle with the tar baby: my hands (or fingers, really) were completely coated with the super-sticky wax, and there was no getting it off. Eventually, I salvaged most of the wax into a little container (I use the metal cups from tea candles), and managed, after repeated washings with turpentine and dish soap, to get most of it off my hands.
So my question, for those who make their own wax, is: is this normal, and if so, how do you deal with the taffy pulling stage? I thought about coating my hands with mineral oil beforehand, but was concerned about knocking the ratios out of whack (I only mixed up a very small batch, as I only had .6 oz [1.5 bars] of rosin).
In the spirit of true scientific method: while I poured the hot liquid into cold water, I pulled it out when it was still warmish; I also didn't let it simmer for 15 minutes as the original recipe stated, as I didn't want it to get too dark. So those are two variables that could have had a negative effect on the outcome.
I should have taken pictures but, by the time it got interesting, were I to pick up a camera, it would have been permanently affixed to my paw. I promise an illustrated step-by-step (and wax for those who want it) the next time I brew up a batch.
thanks,
chris
This is called winter wax -- I made this recipe in particular because, well, it was winter and I was tying steelhead flies. Now it's summer, and as those of you who use wax know, it gets rather runny and isn't particularly user-friendly, particularly in my overheated third-floor tying room. I've been using some cobbler's wax that Ray gave me, but it's quite dark. I've been meaning to whip up a batch of summer wax, and -- encouraged by the impending end of summer -- made up a batch last night.
I tried an 8-2-1 recipe I found in the archives, figuring it would be a little more heat-friendly than the usual summer 7-2-1... and all went well until the 'pull it like taffy stage' (which I hadn't done to my batch of winter wax). To make a long story short, I found myself in a battle with the tar baby: my hands (or fingers, really) were completely coated with the super-sticky wax, and there was no getting it off. Eventually, I salvaged most of the wax into a little container (I use the metal cups from tea candles), and managed, after repeated washings with turpentine and dish soap, to get most of it off my hands.
So my question, for those who make their own wax, is: is this normal, and if so, how do you deal with the taffy pulling stage? I thought about coating my hands with mineral oil beforehand, but was concerned about knocking the ratios out of whack (I only mixed up a very small batch, as I only had .6 oz [1.5 bars] of rosin).
In the spirit of true scientific method: while I poured the hot liquid into cold water, I pulled it out when it was still warmish; I also didn't let it simmer for 15 minutes as the original recipe stated, as I didn't want it to get too dark. So those are two variables that could have had a negative effect on the outcome.
I should have taken pictures but, by the time it got interesting, were I to pick up a camera, it would have been permanently affixed to my paw. I promise an illustrated step-by-step (and wax for those who want it) the next time I brew up a batch.
thanks,
chris
- chase creek
- Posts: 1381
- Joined: Tue Feb 24, 2009 11:00 am
- Location: Ohio
Re: Wax (redux)
Chris, thanks for the post. I'd love to see a step-by-step. My wife has banned me from the kitchen after testing some homemade alcohol stoves (made from pop cans, etc), and I might be able to win my way back into her heart by brewing up some wax. 

"A thing is right when it tends to preserve the integrity, stability, and
beauty of the biotic community. It is wrong when it tends otherwise"
Aldo Leopold
beauty of the biotic community. It is wrong when it tends otherwise"
Aldo Leopold
-
- Posts: 3648
- Joined: Thu Oct 27, 2011 6:28 am
- Location: Southland, South Island, New Zealand.
Re: Wax (redux)
Ah, all very interesting and posing not only a few questions, but also a damn good reason I have not delved into fly tying wax making.
I could see myself with "taffy stage" wax all over the kitchen (well where else would a male of the species heat wax?), through my hair and clothes........ then have to invent some kind of "it wasn't me honey- it was the kids!" story.
Could it be that the 8-2-1 with your rosin of choice made a "watered down" rosin rather than a soft wax? It may be a fine line between "tar baby" hands and a usable product? Perhaps a closer concoction to the 7-2-1 ratio might be more user friendly, half increments instead of whole 7.5-2.5-1?
None of the above is from practical study, just an over active imagination!
Next time, please take photos.
Coleman fuel or white spirits is a good remover of rosin/tree sap from skin. I hold no responsibility for any carcinogenic hydrocabon effects from such practice though!

Could it be that the 8-2-1 with your rosin of choice made a "watered down" rosin rather than a soft wax? It may be a fine line between "tar baby" hands and a usable product? Perhaps a closer concoction to the 7-2-1 ratio might be more user friendly, half increments instead of whole 7.5-2.5-1?
None of the above is from practical study, just an over active imagination!
Next time, please take photos.

Coleman fuel or white spirits is a good remover of rosin/tree sap from skin. I hold no responsibility for any carcinogenic hydrocabon effects from such practice though!

"Listen to the sound of the river and you will get a trout".... Irish proverb.
Re: Wax (redux)
Chris,
Fascinating! I've done some interesting things in the name of fly tying, but have never made my own wax.
Maybe we can get the kids to do the taffy pulling at next year's Rushford event!
Best,
Tim
Fascinating! I've done some interesting things in the name of fly tying, but have never made my own wax.
Maybe we can get the kids to do the taffy pulling at next year's Rushford event!
Best,
Tim
- William Anderson
- Site Admin
- Posts: 4569
- Joined: Mon Feb 23, 2009 3:14 pm
- Location: Ashburn, VA 20148
- Contact:
Re: Wax (redux)
Chris, I've made a few batches of wax myself, but your methods differ from mine and maybe I have some room for growth. My method is to melt down the wax and rosin in an aluminum can cut in half and bent to form a spout (handle with needle nose pliers during operation) and once the wax and rosin are melted I add the pinch of oil (whatever ratio) and stir this around for a couple minutes on a low heat. The concoction never boils or anything. I then simply pour it either into forms or lately I make a long flat "tray" from several layers of aluminum foil and fold up all four sides. Once the wax has completely mixed and blended I pour the contents into the aluminum foil tray. Allow it to cool for hours and remove it from the aluminum foil and slice it up with a really big knife. Toss the can, toss the foil tray clean the knife and the wife is none the wiser. Very clean and quick. Most importantly...clean. The double boiler using the aluminum can in a pot of boiling water is the key.
Now, please help me understand where the idea of pulling taffy and pouring hot contents into cold water comes from. No doubt there are a lot of ways to get the result, and my final product leaves something to be desired, although I like as well as (yes I have a wax collection) all the other waxes I've collected.
Anyone please chime in. Is there something preferable to the taffy or the cold water elements of the process? I'd love to produce a better product, but I'm also in the market for clean and simple.
Thanks for any help. And thanks Chris for spawning another really interesting discussion.
w
Now, please help me understand where the idea of pulling taffy and pouring hot contents into cold water comes from. No doubt there are a lot of ways to get the result, and my final product leaves something to be desired, although I like as well as (yes I have a wax collection) all the other waxes I've collected.
Anyone please chime in. Is there something preferable to the taffy or the cold water elements of the process? I'd love to produce a better product, but I'm also in the market for clean and simple.
Thanks for any help. And thanks Chris for spawning another really interesting discussion.
w
"A man should not try to eliminate his complexes, but rather come into accord with them. They are ultimately what directs his conduct in the world." Sigmund Freud.
www.WilliamsFavorite.com
www.WilliamsFavorite.com
- letumgo
- Site Admin
- Posts: 13346
- Joined: Sat Feb 21, 2009 7:55 pm
- Location: Buffalo, New York
- Contact:
Re: Wax (redux)
Chris - I read your post with great interest. I am happy to see you are still playing around with wax recipes. When I made tying wax, I poured the hot wax into plastic ice cube trays and then chilled the mixture until it was ice cold. I could then strike the ice cube tray on the table and the wax dropped out of the tray as smaller cubes. You can then place the wax cubes into some warm water, to soften them. You may find that you have more control over the wax, if you start with the cold wax, and warm it until it becomes pliable. Beyond a certain working temperature, the mixture will become very soft and very sticky.
How does you wax behave at current room temperature? Is it still soft and sticky?
Keep in mind, that each wax blend will have an ideal working temperature range. The normal working temperature range will be in the range of 65°F (room temperature) to 98°F (body temperature). I have some waxes that only work well at the lower temperature ranges. These waxes do not like to be handled. In other words, they work best when they are colder, and I generally do not keep them in my hand when tying. Otherwise, they become too soft and sticky, when they warm to body temperature. I generally set these types of wax down after each use.
If the wax does not behave the way you want, you can always remelt it and adjust the formula to change the properties more to your liking.
When I was at Roscoe, I noticed that William had a useful method for managing his tying wax. He had multiple small balls of wax, that he could pick up and use as he was making dubbing brushes. After a few uses, he would switch to another piece, setting down the first piece to let it cool and firm up. I thought it was an interesting approach, and made note of it for future tying cessions.
The piece of cobblers wax was from another member of this forum, Bill Bailey (screen name wsbailey). Bill makes a bunch of different tying waxes (dark and light cobblers wax, tyers wax, and liquid wax, which you put on the thread with a bodkin). I've used all of Bill's waxes, and found them to be excellent. Perhaps Bill will chime in and share some advice.
When I tried making cobblers wax, I ended up with mixtures that were a little too "dry" for my tying preference. I believe that I had a little too much resin in my blend. Once I tried Bill's cobbler wax blend, I gave up on my cobblers wax experiments.
I look forward to hearing more about your wax making adventures. Hearing the stories of what does not work, is just as interesting as what works. All part of the fun of learning.
How does you wax behave at current room temperature? Is it still soft and sticky?
Keep in mind, that each wax blend will have an ideal working temperature range. The normal working temperature range will be in the range of 65°F (room temperature) to 98°F (body temperature). I have some waxes that only work well at the lower temperature ranges. These waxes do not like to be handled. In other words, they work best when they are colder, and I generally do not keep them in my hand when tying. Otherwise, they become too soft and sticky, when they warm to body temperature. I generally set these types of wax down after each use.
If the wax does not behave the way you want, you can always remelt it and adjust the formula to change the properties more to your liking.
When I was at Roscoe, I noticed that William had a useful method for managing his tying wax. He had multiple small balls of wax, that he could pick up and use as he was making dubbing brushes. After a few uses, he would switch to another piece, setting down the first piece to let it cool and firm up. I thought it was an interesting approach, and made note of it for future tying cessions.
The piece of cobblers wax was from another member of this forum, Bill Bailey (screen name wsbailey). Bill makes a bunch of different tying waxes (dark and light cobblers wax, tyers wax, and liquid wax, which you put on the thread with a bodkin). I've used all of Bill's waxes, and found them to be excellent. Perhaps Bill will chime in and share some advice.
When I tried making cobblers wax, I ended up with mixtures that were a little too "dry" for my tying preference. I believe that I had a little too much resin in my blend. Once I tried Bill's cobbler wax blend, I gave up on my cobblers wax experiments.
I look forward to hearing more about your wax making adventures. Hearing the stories of what does not work, is just as interesting as what works. All part of the fun of learning.
Ray (letumgo)----<°))))))><
http://www.flytyingforum.com/index.php? ... er=letumgo
"The world is perfect. Appreciate the details." - Dean
http://www.flytyingforum.com/index.php? ... er=letumgo
"The world is perfect. Appreciate the details." - Dean
Re: Wax (redux)
Sorry about the delay in getting back to this... but I had to dig out the camera to begin to answer William's question. More on that later.
First, on kitchens: we have an great big old (circa`1890s) house (such things are affordable in Western NY, as long as one has some DIY aptitude). The third floor is a separate apartment, which has both a separate door to the outside as well as access from our second floor. Someday it will probably be a mother-in-law apartment for one of our MiLs, but until then it serves several other purposes: it's the poker den / library / reading room, and my wife and I have our offices there. Since I work more at home than she does, I got the big one... which is actually quite huge, and contains a kitchen and sink. And a turret.
Needless to say, it's where I do my tying as well... so I have access to a kitchen without serious repercussions should things go terribly awry. And a bunch of pots I picked up at a garage sale.
Second: onto commenting on the wax itself. I should preface all of this by explicitly stating that I have made tying wax exactly twice before, and so should by no means be considered an expert. I'm just reporting my findings, musings, researches and results...
On the taffy stretch:
William asked why do the stretch and why the immersion in cold water. My answer is because, according to my research, that's how many of the elders did it -- and therefore a great place to start. Here is a quote from Leisenring's wax chapter, quoted from this board (http://www.flymphforum.com/viewtopic.ph ... ffy#p48791)
"Melt one-half pound of the best white turpentine resin, add one ounce of pure white beeswax which should be pared off or chopped up into small pieces. Simmer for fifteen minutes, allowing it to melt and mix thoroughly with the resin. Now add one-half ounce of fresh lard and stir slowly while the mixture simmers just below the boiling point for another fifteen minutes. (Note: when stirring this simmering wax remember that it is extremely inflammable and therefore dangerous. The safest and best stirring implement is a stick about eighteen inches long and somewhat smaller in diameter than a lead pencil.)
Pour this liquid wax into a basin of water. Do not touch it until it has had a chance to cool because your fingers will be badly burned. After it has cooled enough to permit handling, pull at it and work with it, as taffy pullers do with taffy, until it has a light color and even texture. You will find it necessary to immerse it in warm water in order to make it pliable enough to work."
It is a 1940s text, _Professional Fly Tying, Spinning and Tackle Making: Manual and Manufacturers' Guide_, reproduced on the FAOL site (I didn't post the link because I'm not sure what the board policy is on such things; the original online source is easily found by googling a stretch of several words):
"In Britain, soft tacky wax is usually made as follows: Take two parts by weight, of the best resin (clean burgundy pitch if you can get it, but any resin will do) and one-fourth part, by weight, of clean tallow or lard. Melt this blend for fifteen minutes. When the ingredients are well fused together, pour the wax into a pail of cold water and work it up well with the fingers until it is tough and pliable. The more it is pulled and worked, the better it turns out. Break it up in pieces suitable for use and keep them in a jar of water. If the wax is too hard or brittle, melt it again and add more tallow or lard; if it is too soft, or not tacky enough, add more resin. To clean your fingers of wax, use methylated spirits of alcohol or any dry-cleaning preparation."
I suspect the taffy stretching has something to do with unwanted crystallization, but I'm just extending what little I know about candymaking. Stretching would (should?) bring in elasticity and decrease hardness and, I suspected anyway, make what would have been a hard recipe (8-2-1) a little softer without decreasing the resistance to temperature. Finally, I stretched it because the recipes said to stretch it - and I was curious.
I can't say I succeeded, but that I don't know enough to know what, exactly happened. However, I can illustrate what it looked like with and without stretching:
This is what the recipe looks like without stretching:
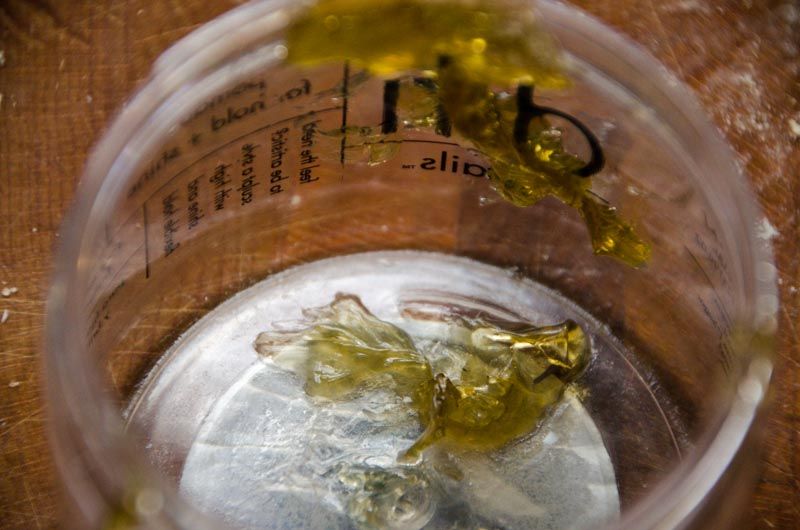
(I used this container for the cooling bath, and this is what adhered to the sides). It's much harder than the pulled wax, but is certainly seems quite usable. It's sticky, but not to the level of the pulled stuff. It can be pulled off the container and rolled into a ball for use, leaving a sticky residue behind on my skin, but not unusually so. I haven't used it yet, but anticipate trying it soon.
This is the post stretching material. The aluminum tea candle holder is somewhat of a disaster, as I tried to use it to scrape off some of the goo from my hands. I usually try to be much neater.
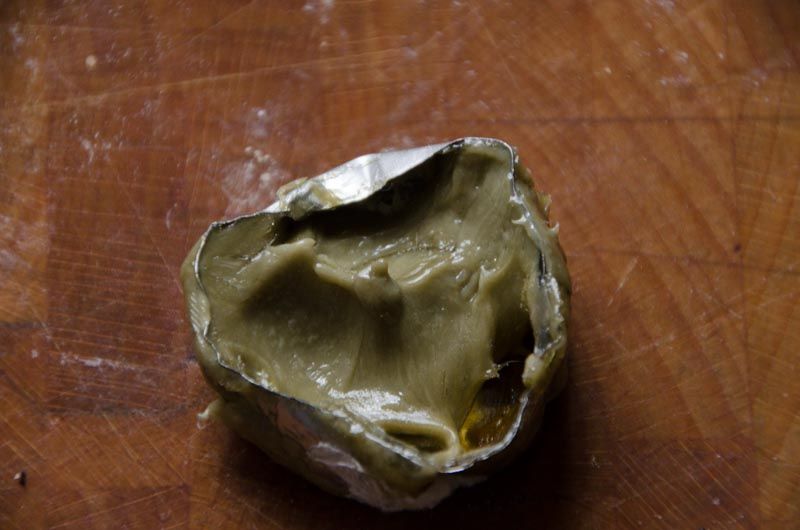
(you can see, in the lower right corner, some of the unpulled material as well).
You can see that it's radically different from the other stuff. I suspect the difference is in some way that the pulling changed the crystalling structure (perhaps) and (for sure) folded air into the mixture.
This stuff could be licensed for non-lethal crowd control. It's really sticky. In fact, in an attempt to compare it to the unpulled mixture I just tried to roll some into a ball... and wound up pulling out the zippo lighter fluid again. Late last night, however, it was about 10 degrees cooler in my office, and it seemed a little less virulently sticky. Interesting.
If we tried to use it, or do a wax pull, at the kid's tying event, Tim, we'd have one big ball of kidwax -- at least until nightfall. I'm not sure how the parents would react...
I suspect that had I heated it longer, it would have altered the crystalline structure or some such thing, and may have led to greater success. I'll test this at some future date.
Thanks go to Ray for sharing William's tip on switching between different wax balls! That's a good one, although I want to be able to leave it on my knuckle through a long tying session without having to worry about it. I use it not just for dubbing, but for ensuring the thread goes exactly where I want to and stays there... it's pretty useful, especially when dealing with slippery materials and hairwings and such. This batch might be good for dubbing-only use, if one could find a way to apply it to thread without actually touching it!
I really liked the Bill Bailey cobbler's wax you gave me, Ray -- but it darkened the thread significantly, which wasn't a big deal until I had to tie sulphurs and cahills...
The next step is to brew up several recipes, do pull and non-pulled versions, and see what happens. I'll definitely try Leisenring's recipe, which seems to be quite different from many of the ratios I have seen before (16-2-1!!).
It'll require a significant amount of rosin... Has anyone used raw pine gum rosin, rather than (refined) bow rosin? It would be significantly cheaper, and the local high school string sections might be happier if I didn't buy out WNY's entire stock of bow rosin...
First, on kitchens: we have an great big old (circa`1890s) house (such things are affordable in Western NY, as long as one has some DIY aptitude). The third floor is a separate apartment, which has both a separate door to the outside as well as access from our second floor. Someday it will probably be a mother-in-law apartment for one of our MiLs, but until then it serves several other purposes: it's the poker den / library / reading room, and my wife and I have our offices there. Since I work more at home than she does, I got the big one... which is actually quite huge, and contains a kitchen and sink. And a turret.

Second: onto commenting on the wax itself. I should preface all of this by explicitly stating that I have made tying wax exactly twice before, and so should by no means be considered an expert. I'm just reporting my findings, musings, researches and results...
On the taffy stretch:
William asked why do the stretch and why the immersion in cold water. My answer is because, according to my research, that's how many of the elders did it -- and therefore a great place to start. Here is a quote from Leisenring's wax chapter, quoted from this board (http://www.flymphforum.com/viewtopic.ph ... ffy#p48791)
"Melt one-half pound of the best white turpentine resin, add one ounce of pure white beeswax which should be pared off or chopped up into small pieces. Simmer for fifteen minutes, allowing it to melt and mix thoroughly with the resin. Now add one-half ounce of fresh lard and stir slowly while the mixture simmers just below the boiling point for another fifteen minutes. (Note: when stirring this simmering wax remember that it is extremely inflammable and therefore dangerous. The safest and best stirring implement is a stick about eighteen inches long and somewhat smaller in diameter than a lead pencil.)
Pour this liquid wax into a basin of water. Do not touch it until it has had a chance to cool because your fingers will be badly burned. After it has cooled enough to permit handling, pull at it and work with it, as taffy pullers do with taffy, until it has a light color and even texture. You will find it necessary to immerse it in warm water in order to make it pliable enough to work."
It is a 1940s text, _Professional Fly Tying, Spinning and Tackle Making: Manual and Manufacturers' Guide_, reproduced on the FAOL site (I didn't post the link because I'm not sure what the board policy is on such things; the original online source is easily found by googling a stretch of several words):
"In Britain, soft tacky wax is usually made as follows: Take two parts by weight, of the best resin (clean burgundy pitch if you can get it, but any resin will do) and one-fourth part, by weight, of clean tallow or lard. Melt this blend for fifteen minutes. When the ingredients are well fused together, pour the wax into a pail of cold water and work it up well with the fingers until it is tough and pliable. The more it is pulled and worked, the better it turns out. Break it up in pieces suitable for use and keep them in a jar of water. If the wax is too hard or brittle, melt it again and add more tallow or lard; if it is too soft, or not tacky enough, add more resin. To clean your fingers of wax, use methylated spirits of alcohol or any dry-cleaning preparation."
I suspect the taffy stretching has something to do with unwanted crystallization, but I'm just extending what little I know about candymaking. Stretching would (should?) bring in elasticity and decrease hardness and, I suspected anyway, make what would have been a hard recipe (8-2-1) a little softer without decreasing the resistance to temperature. Finally, I stretched it because the recipes said to stretch it - and I was curious.
I can't say I succeeded, but that I don't know enough to know what, exactly happened. However, I can illustrate what it looked like with and without stretching:
This is what the recipe looks like without stretching:
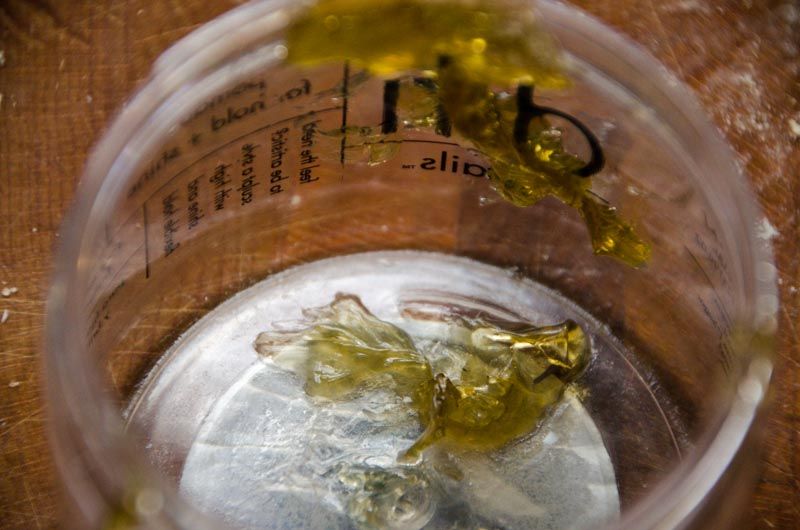
(I used this container for the cooling bath, and this is what adhered to the sides). It's much harder than the pulled wax, but is certainly seems quite usable. It's sticky, but not to the level of the pulled stuff. It can be pulled off the container and rolled into a ball for use, leaving a sticky residue behind on my skin, but not unusually so. I haven't used it yet, but anticipate trying it soon.
This is the post stretching material. The aluminum tea candle holder is somewhat of a disaster, as I tried to use it to scrape off some of the goo from my hands. I usually try to be much neater.
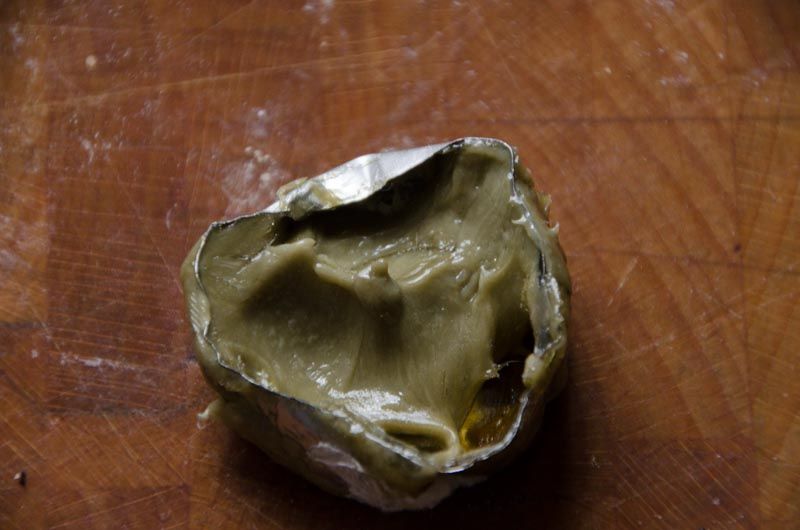
(you can see, in the lower right corner, some of the unpulled material as well).
You can see that it's radically different from the other stuff. I suspect the difference is in some way that the pulling changed the crystalling structure (perhaps) and (for sure) folded air into the mixture.
This stuff could be licensed for non-lethal crowd control. It's really sticky. In fact, in an attempt to compare it to the unpulled mixture I just tried to roll some into a ball... and wound up pulling out the zippo lighter fluid again. Late last night, however, it was about 10 degrees cooler in my office, and it seemed a little less virulently sticky. Interesting.
If we tried to use it, or do a wax pull, at the kid's tying event, Tim, we'd have one big ball of kidwax -- at least until nightfall. I'm not sure how the parents would react...

I suspect that had I heated it longer, it would have altered the crystalline structure or some such thing, and may have led to greater success. I'll test this at some future date.
Thanks go to Ray for sharing William's tip on switching between different wax balls! That's a good one, although I want to be able to leave it on my knuckle through a long tying session without having to worry about it. I use it not just for dubbing, but for ensuring the thread goes exactly where I want to and stays there... it's pretty useful, especially when dealing with slippery materials and hairwings and such. This batch might be good for dubbing-only use, if one could find a way to apply it to thread without actually touching it!
I really liked the Bill Bailey cobbler's wax you gave me, Ray -- but it darkened the thread significantly, which wasn't a big deal until I had to tie sulphurs and cahills...
The next step is to brew up several recipes, do pull and non-pulled versions, and see what happens. I'll definitely try Leisenring's recipe, which seems to be quite different from many of the ratios I have seen before (16-2-1!!).
It'll require a significant amount of rosin... Has anyone used raw pine gum rosin, rather than (refined) bow rosin? It would be significantly cheaper, and the local high school string sections might be happier if I didn't buy out WNY's entire stock of bow rosin...
Re: Wax (redux)
Quote It'll require a significant amount of rosin... Has anyone used raw pine gum rosin, rather than (refined) bow rosin? It would be significantly cheaper, and the local high school string sections might be happier if I didn't buy out WNY's entire stock of bow rosin... Quote
If you use raw resin there is a chance of explosion because of the turpentine coming out the resin. So melt it outside and be careful
greeting
If you use raw resin there is a chance of explosion because of the turpentine coming out the resin. So melt it outside and be careful
greeting
There will allways be a solution.
http://www.aflyinholland.nl
http://www.aflyinholland.nl
Re: Wax (redux)
Ray asked if I could add something to the discussion so here goes. I have made every wax that I could find in fly tying literature. A lot of it ended in the trash. A lot of it. Making wax is tricky business and can be downright dangerous. The easiest and most reliable recipe is Marvin Nolte's tying wax. It's the 7-2-1 wax already mentioned. Fly tying literature has many examples of wax similar to the one Leisenring mentioned in his book. Ogden and Francis Francis are two sources that come to mind. These waxes are stickier than Nolte's wax and all require being pulled like taffy. Pulling the wax not only helps mix the ingredients it also makes the wax stronger. When you can pull the wax until it no longer breaks as it is stretched then it is ready. There is no reason to use bow rosin. Google gum rosin and look for WW grade. Bill
Re: Wax (redux)
The refined rosin in a baseball pitcher's rosin bag worked well when I used it for making wax, and it is not prohibitively expensive when you can find it at a sporting goods store.
Some of the same morons who throw their trash around in National parks also vote. That alone would explain the state of American politics. ~ John Gierach, "Still Life with Brook Trout"